Since I didn’t have my laptop, I didn’t write up a daily summary of events so this is going to be a bit less narrative and a bit more stream-of-memory.
The first day, things did not go particularly well. The problem appeared to be heat – not enough of it. The interior of the smelter ought to be yellow-white hot, for about 5 hours. You charge the crucibles with iron and carbon, cap them off with refractory, and melt the contents a bit. The carbon is provided by charcoal (mesquite-flavored blade!) and the iron is electro-smelted raw iron [ebay] – if the iron we were using were our own reduction from iron sands, that would be called ‘tamahagane’ and it’s the ne plus ultra of Japanese metallurgy. Let me put it this way: master swordsmiths can count the number of times they encounter tamahagane; it’s rare, it’s ridiculously expensive, and it’s probably indistinguishable from oroshigane once it’s compiled into a blade. When I say “ridiculously expensive” the metal used in the blades we made would have cost thousands of dollars if it were tamahagane. Basically, the electro-smelted and refined stuff is taking the easy way out.
Another way of taking the easy way out is a technique that is popular in eastern Europe, called ‘bulat’ – you charge the crucible with drill bits or bits of brake disc – it’s already steel, you’re just compositing your own brew of the stuff. Bulat is close spiritually and technically to true Damascus steel, AKA “wootz” which was made by ancient smiths who charged their crucible with broken bits of other people’s weapons or whatever. I don’t know how it’s done but apparently scientists can track the origins of some kinds of metals, so it’s been possible to tell that some wootz billets included steel from Northern India, China, and Irish bog iron in the same blade. Basically, steel followed the silk road.
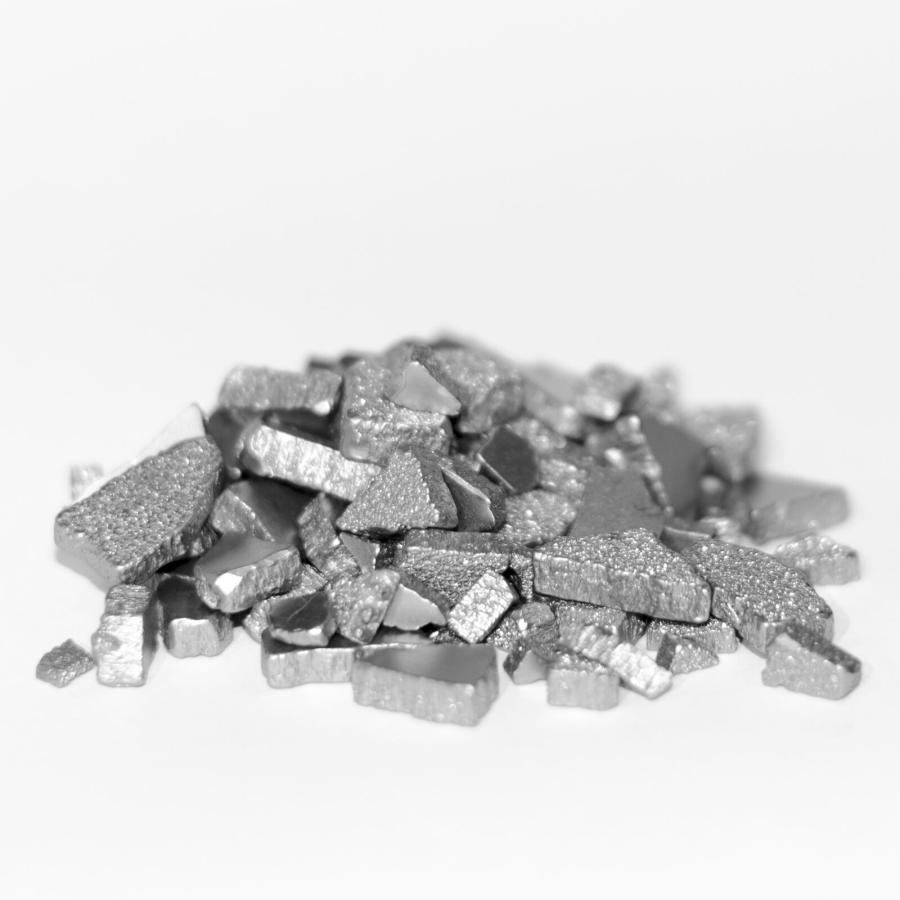
electro-smelted pure iron, ebay
I’m planning to eventually experiment with some wootz of my own, so this class on oroshigane was well-timed.
Sampson is well, which made me very happy. He’s remarkably mellow and has just gotten mellower. I wonder if he remembered me, or if he’s just so chill and friendly with everyone. It was nice to be able to take a break every so often and go rub a dog’s nose. The charcoal we used to charge the crucibles had a mesquite scent and I made sure it smelled slightly doggy, too.
Setting the crucibles in the smelter and turning it on full blast, we then had 5 hours to sit around and shoot the breeze waiting to see how it came out. The next morning we checked and – it didn’t. There wasn’t enough heat, so the crucibles’ contents looked unchanged. So, what to do? Open the gas to maximum, air to maximum, and try again. One of the problems we had the first day was the propane tank started to freeze up, so the second day was spent pouring boiling water into a towel wrapped around the bottom of the tank. That may or may not have helped.
The morning haul on monday was a bunch of pucks of melty iron that had absorbed the carbon they were baked with. Next stage in the process is to consolidate those into a bar, then begin folding and further consolidating the bar – a lot of what’s going on in that process is carbon migration and carbonization of regions of iron that have not yet converted to steel.
That’s probably a good place to stop for now.
When you hear about all the problems people are having with fueled furnaces, electric smelters start to look pretty attractive.
That made me wonder if there are people building arc furnaces in their backyard.
(Spoiler alert: of course there are.)
Thank you!
Interesting about identiying the origin of the different irons in wootz. There has been an incredible expansion in what we can find out with chemical analysis, and in how little (comparatively, and actually) it costs to do so. DNA analysis is now so cheap that archaeologists are having the earth of caves where some hominin lived, as evidenced by simple stone tools, analysed to find out which of them it was. I may have mentioned this before, but it is so cool that we can say it was the same one through out a caves use or conversely that it was a series of diferent ones or that different ones used the cave repeatedly over the centuries or millenia the cave was in use. It’s just fucking incredible the progress that has been made in that area of science.
Awwww Sampson having a nap.
rsmith@#1:
When you hear about all the problems people are having with fueled furnaces, electric smelters start to look pretty attractive.
All of the big commercial outfits use electric smelters. It’s much easier to control the heat, and you can build them in a nice cabinet with a controlled atmosphere and a robotic stirrer/manipulator.
other than being rare, is tamahagane actually any better than high end commercial steels? i remember hearing something about it being better for hamons since it can lack manganese.
looks like a very cool project!
There are some amazing steels being produced currently.
I may be wrong on this, but I’m under the impression that iron sands were used in Japan because the more easily refinable iron ores that are typically used, were not as common, due to the geology of the Japanese Islands. (It’s been a while since I’ve read up on metallurgy or smithing, or studied geology, so…)
So, while it might be a neat exercise for the sake of tradition or building something from the ground(literally)-up, it won’t reliably result in a higher quality steel that what you could get off of ebay or amazon, or possibly even Home Depot…
Plus, it’s a lot more work, energy, effort, time, and all that.
Modern steels are very good, and are generally better than anything historical. If nothing else, they are more consistent, and due to that consistency, people can figure out the best way to heat treat them reliably, etc.
Probably one of the contributing factors to me quitting reddit, was me getting tired of arguing about carbon vs stainless steel for knives on the survival and bushcrafting forums, so much nonsense in those subs…
OT: This sounds tasty, and I would try it –
Gaia-Sausage-Enceladus
maybe with a nice balsamic dressing.
lochaber@#5:
I may be wrong on this, but I’m under the impression that iron sands were used in Japan because the more easily refinable iron ores that are typically used, were not as common, due to the geology of the Japanese Islands.
That is correct. In Northern Europe, for example, bog iron was used instead. I still think that was just trace amounts.
The Japanese, typically, took a difficult and time-consuming process and pointed and said, “we planned it that way.”
Modern steels are very good, and are generally better than anything historical. If nothing else, they are more consistent, and due to that consistency, people can figure out the best way to heat treat them reliably, etc.
Correct. But, but but… An oroshigane blade like this is going to have a lot of the durability of wrought iron, from the way the carbon layers and slag are interspersed. Depending on how it’s done, there won’t be any stress-lines that form cracks, because those have been repeatedly worked out. I doubt any of this matters much, but I am absolutely sure you will recognize the results look a whole lot better than a monosteel.
By the way the current state of the art is to use sintered metals and that allows precise composition of results. For example, you could use powder processes to produce a blade with a malleable iron back and a tungsten carbide edge. Someone could.
Probably one of the contributing factors to me quitting reddit, was me getting tired of arguing about carbon vs stainless steel for knives on the survival and bushcrafting forums, so much nonsense in those subs…
I don’t think I could bear those discussions. Really, so much annoying there. Depending on what you’re doing you’ll want different kinds of blades. It would take high-level stupid to use a nihonto to chop wood for survival purposes. For a survival knife, whatever gets the job done is the order of the day. And, personally, I think “survival” means having a working cell phone and a functioning brain – the knife is much less important unless it’s a chainsaw.
jazzlet@#2
A handheld X-ray fluorescence device can (nondestructively) tell you pretty precisely what the composition of an alloy is. It can detect all kinds of atoms from aluminum to uranium.
dangerousbeans@#4
Probably depends on what your definition of “better” is.
Modern steelmaking can produce consistent quality, even in large batches. I think it is fair to say that in earlier times it was more of a hit-or-miss process. And that’s not meant as disrespect to traditional craftspeople. There is a series of youtube videos by Niels Provos where he and some friends try to make wootz steel. It’s not easy.
Powder metallurgy can make fine-grained alloys with small carbide particles that are not possible with traditional steelmaking.
@rsmith
yeah, there’s always the questions of definitions.
this does look like a far more interesting way to get steel than just calling the supplier
dangerousbeans@#10:
this does look like a far more interesting way to get steel than just calling the supplier
I see it as rounding off my knowledge of the craft. Now, if I decide, “I’ll just chop off a piece of W-2 and make a paring knife out of it” it’s a choice not the only option. FWIW there are tamahagane paring knives out there, but that’d be considered overkill, like making a blade out of pure pimp-metal. A paring knife of W-2 is going to be just fine for paring. A paring knife of tamahagane would work as well, but no better, though someone might value knowing about the historical process and the difficulty involved in its making.
The steel for a W-2 paring knife is about $5. The steel for a tamahagane paring knife would be around $400.
dangerousbeans@#10
It is certainly labour intensive in a way that is hard for us to comprehend.
Dr. Devereaux at acoup.blog ran a series about pre-modern iron and steel production.
Going by his numbers, for every kg of iron, you’d need about 12 kg of ore and 105 kg of wood. (Most of the wood is converted to charcoal.)
Considering his example that a late Roman republic Legion would have carried around 44000 kg of iron, having to gather and process all that with hand tools and manpower is quite the job.
I feel, at this point, that I should say: I do not feel that art is inherently more valuable if it’s hard to make. In fact, most of the things humans make have details that are hard, and make a lot of difference between an OK ${whatever} and a great one. It is up to the viewer/consumer to decide what they appreciate, and whether knowing something was hard to make affects their impression of it.
My opinion is that the subtle watering in oroshigane steel is beautiful. I like W-2 for its practicality, but I don’t think it’s on the same plane in terms of appearance. I suspect a W-2 blade would perform comparably in terms of cutting (that’s all about the grind-lines) and strength, if it was differentially quenched. That’s also a skill that makes a difference.
I suppose I could do a post on differential quenching and its impact on a few pieces of W-2 but that would involve making some sacrificial pieces and I feel like that’s a waste.
The question of “what is beautiful, and when and why?” is one I do not choose to leave to philosophers because I feel that they are largely useless wankers and an approach from nihilism works just as well.
I just did a bit of searching around. It turns out there’s a bunch of “tamahagane” knives that are machine-made stainless. That’s, uh, nevermind.
Sometimes it’s the little things.
Years ago I bought a simple Robert Herder carbon steel paring knife. It’s not big; the blade is only 8 cm. It has a triangular cross-section and it’s very thin; the spine is only 1 mm thick.
It’s wicked sharp and only needs occasional stropping to stay that way.
This quickly became my go-to kitchen knife. Best € 12,- I ever spent, I reckon.
It exiled more expensive knives to the back of the drawer. It does need to be rinsed and dried after use, but that’s not a big deal.