Where I left the damascus-twister, it was mostly an idea and a pile of parts.
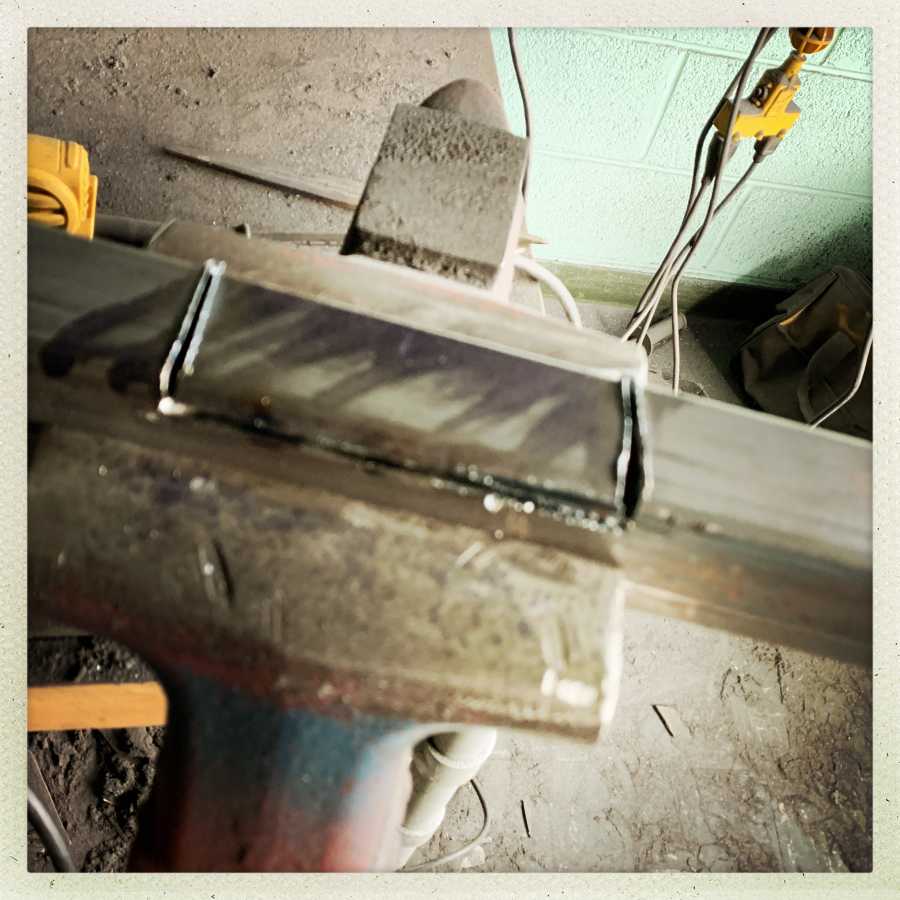
oh look it’s out of focus!
That rough cut, done with an angle grinder and a diamond wheel, was painful to look at. At some point or other I thought, “I should have someone do that on a milling machine.” Oh, wait, like the milling machine right behind me?
It didn’t take any fancy machining; I just cut a rectangular box with straight edges and it was amazing how much better it looked after that.
Mild steel responds well to a wire brush and some WD-40. If I had been clever enough to just use the milling machine in the first place, and not run around chopping chunks out of the metal with an angle grinder, it would look “professional” but instead maybe it looks “rugged” or something. [Actually it speaks to my subconscious saying “be careful there might be razor-sharp edges in this piece of sloppy-ass thrown-together kludgework”]
As you can see, I’ve drilled holes for bolting the head into the bar, and it’s waiting for me to make a run to the bolt library at Ace Hardware in Clearfield; in my pocket I carry a bolt of the right size (but wrong length) with the correct length scratched onto it with a carbide drill-bit. I have a nice pair of Mitotuyo calipers for measuring stuff like that, but if I can eyeball a thing, that’s how I’ll probably do it.
This is how it call came together:
I could have trued the wrench head up a bit with the milling machine but I just hit it on the belt sander and made it flat until it slid nicely into the housing. So, that’s it!
The next part was hard(er) – in order to test it properly, I had to whip up a bar of damascus to twist. In the past, when I’ve twisted a bar using a wrench, the thickness of the bar has been limited by the leverage I can apply. In this case, I am assuming I have a lot more leverage, with that great big 4-foot lever. (I guess technically that is 2 2-foot levers) I’m ballparking that at a 24:1 mechanical advantage, which means that I can put about 4,800lb of “oomph” into my twist – that’s why I made this thing solid; I do not want something to snap and send me flying into my work-piece face-first, or stumbling around the room in a random direction. Actually, I am most likely to snap the welds on the post my vise is mounted on, which would also be bad.
I made a smallish stack of 15N20 and some 1095 and tacked it together with the MIG, then fluxed it and put it in the forge to heat for about a half hour. After that, I started pressing it with a drawing die, squashing it into a longer and rounded thing about an inch in diameter.
The welds don’t have to be particularly good; they just have to hold together until the first couple compressions, after which the stack will be on its way to becoming a bar that is a single piece of steel.
As I was doing this, I had time to think, and I realized that twist damascus was probably invented as a way of making sure a piece of steel was homogenous. If there are missed spots in the weld, they are going to come under tremendous pressure when the steel is twisted; they might stick. Or, if they don’t it’s not as if the piece of steel is going to unwrap itself under anything less than heinous pressure. A knife-wielder does not need to worry about a piece of twist damascus untwisting on them – they’d disintegrate first.
I set up a camera, and wrapped a go pro around the bar, and gave it a go.
Everything worked perfectly. It twists so hard that I did worry about my vice’s grip slipping. The spring-loaded one-way catch on the wrench piece worked wonderfully – I did not need to fart around getting it to grab, and to ungrab, I just gave a little turn the other direction, while lifting slightly, and it unlocked.
Reminder: be careful not to put my belly up against the yellow-hot bar. I also like the fact that the lever-bar sits between me and the hot metal; if the hot metal takes a hit and comes free, that could be very helpful. And I also noticed that digital cameras appear to pick up some different part of the spectrum; they don’t record the bright yellow bar correctly and turn it a sort of evil purple color.
Here’s what it looked like from the GoPro:
The jaws of the wrench came through OK; they got hot but the steel facings held up fine. Perhaps if I were doing big production runs of twist, heat build-up would be a problem.
End result: a 1″ square bar, 12″ long of low-layer high twist damascus. I think I’ll saw it up into a couple pieces and turn those into wood-turning chisels. To do that, I will make my own die for the hydraulic press, so I can squash a steel bar into a curved gouge-shape.
Elsewhere: the suminigashi bar that I made to serve as the support for a carbide cutter has turned out to be ridiculously tough. I blew up a half-dozen drill bits trying to make an impression on it, and finally resorted to heating one end to red hot and drilling it while it was hot. That succeeded but the drill bit was mostly melted. I let the bar anneal then cleaned the hole up with a new drill bit and proceeded to snap an 8/32 tap off in the hole: it’s not just undrillable, it’s untappable. I may give up on the idea of using fancy damascus for the carbide rake; I have some nice clean 1/2″ x 1/2″ O-1 tool steel that would be a lot more tractable.
And it focuses better, too!
When I saw the title of this blog post, I was really puzzled. “Kunst” means “art” in German. “Grabber” was obvious, but what was “wister” supposed to be?
I noticed that there’s a word “twister” in the middle only after looking at the video where the name was “knunstwistergripper” instead.
The moment my brain had already identified “Kunst” as a word, I failed to see how the letter “t” could belong to “twister.”
Andreas Avester@#2:
The moment my brain had already identified “Kunst” as a word, I failed to see how the letter “t” could belong to “twister.”
I was just playing with words, twisting them around, hammering them into new shapes. “It seemed like a good idea at the time” is my only excuse. No, wait, Rudy Giuliani came up with the name for that…
I have a typo on the title of the youtube video. I left it there. The interface on youtube makes me head hurt; I think it’s an experiment to see how much shit people will put up with if the shit is “free.” Fixed now.
Reginald Selkirk@#1:
And it focuses better, too!
I just shaved a few hundreds off and it brought the focal plane in! I felt stupid for not thinking of that before.
“The moment my brain had already identified “Kunst” as a word, I failed to see how the letter “t” could belong to “twister.”
I know the problem. A couple of days ago I saw an advertising sign with “couteau” embedded in a silly name and could not seperate “cout” from the “eau”.
Not going to lie, the title had me thinking the Germans had a word for the Hamberdler.
Angle grinders appear to be the Visual BASIC of metalworking, i.e. always the right answer.
Nice. Looks like it did the expected job well enough.
And the color distortion with the GoPro is pretty cool…
[What Tabby wrote]
“that great big 4-foot lever. (I guess technically that is 2 2-foot levers) I’m ballparking that at a 24:1 mechanical advantage”
huh? 24-to-? oh, American
twisting does seem like a good way to homogenise bloomery type steels. could it also deform any slag inclusions into shapes that are less likely to cause problems? whereas if you just folded it you might have a flat plane that could cause delamination?
That looks quite impressive. (For some reason, I expected you hold the bar horizontally and rotate the Kunstgrabgetwister in a vertical plane. It seems a lot safer the way you’re doing it.)
The color tint is given by the fact that camera sensors are very sensitive to near-infrared. They have very good IR filters, but your yellow-hot bar is incredibly bright in infrared, so some of that leaks through. You can also use your phone camera to check that an infrared remote works: the IR LED appears the same purplish color. I think it appears purple and not white because white visible light contains more green than blue and red, but is represented as equal R, G, B numbers, so the gain of the red and blue channels is higher than that of the green. The IR makes it through all three colored filters equally, so it is registered at a lower intensity in the green channel.
If you have one of those old three-CCD cameras, you may be able to capture something closer to the actual color. Ordinary color film works too.
Andrew Molitor @ #7:
Angle grinders appear to be the Visual BASIC of metalworking, i.e. always the right answer.
Ew. Ew!
cvoinescu@#11:
I expected you hold the bar horizontally and rotate the Kunstgrabgetwister in a vertical plane. It seems a lot safer the way you’re doing it.
This may not be a valid theory but it’s one I’ve been following: I think that if you plan your movements to be horizontal, then if ${whatever} gets away from you, it will tend to move in a horizontal plane. That means if you are using an angle grinder and you have your arms bracing it horizontally, it can’t (?) kick vertically toward your face – but if you are using it so your arms are moving vertically then you are actually facilitating it kicking toward your face. From the video you can see that my twisting thing is powered by my feet, not my arms. So I am using my weight and my hips, walking in a circle, which is very stable. if the thing pops off or the bar pops out of the vice, I don’t see any way it pops toward my face.
The main danger I see still (but it’s general) is losing a grip with a tong and having the piece of yellow hot steel fall on my foot. I am aware of that danger at all times and am ready to dance like Fred Astaire.
dangerousbeans@#10:
could it also deform any slag inclusions into shapes that are less likely to cause problems? whereas if you just folded it you might have a flat plane that could cause delamination?
Yes, except it also moves a weld that didn’t take into 3 dimensions, so it can’t be ground out. I think it’s a win in the long run, though.
The part about this that is weirdest is the way the molecules move at welding temperature. They just squish and spin and the bar doesn’t get thinner or twist off or anything like it; it just moves around.
I guess at forge welding temperatures the steel is starting to give up on being a solid. i really need to get set up to start trying some forging
oh, i wonder how quickly hot steel goes through a good boot? might be worth testing if any of us have an old pair
dangerousbeans@#15:
oh, i wonder how quickly hot steel goes through a good boot? might be worth testing if any of us have an old pair
I’ve been wearing timberland eurohikers, which are pretty heavy leather. I do have a set of steel toed engineer’s boots that I plan to replace the eurohikers with, eventually (they’re the boots I wore to Chernobyl…) I don’t want to retire them yet, though I suppose I could put a thermometer in one and drop a billet on the toe. For science. Seems like something I don’t want to know.
Very clever design and it seems to work well.
As for the footwear, testing it seems like a good idea to me. Better to know, than end up with a third degree burn to the top of your foot. I found this regarding what to look for in a good welder’s boot. https://www.safetyshoestoday.com/en/applications/safety-shoes-for-welders
yeah it’s not something i really want to know, but it’s also something that if i do learn it i want to learn it in a planned, controlled way