As I mentioned [stderr] my first attempt at feather damascus was a bust, and left me with a half-split half-welded block of many-layered metal. Some gears in my subconscious clicked and I realized there was some symbolism there in the metal.
Kestrel’s a much better artist than I am, and rendered for me a copy of a heart drawn in the style of Caine.
I heated the chunk of steel and mashed it flat(ter) and kind of evened it up, then spray-primered it, cut out the heart-shape, traced the outline, and cut it from the bar.
I did not manage to take any photos of the shape-cutting process, because it was messy and didn’t look like much – I cut the edges with a cutoff wheel in an angle grinder, and kept cutting them closer and closer until I could switch to a grinder wheel.
Getting the notch at the top was a pain; I had to shape it in with a grinder wheel and I needed to be careful not to hit the other side and gouge a chunk out of it.
To make the hole, I used an endmill on the Bridgeport. Unfortunately, somewhere in the process of all the whacking and cutting and grinding, the steel had work-hardened considerably. The first mill snapped so I made a little hot-spot with the oxy/acetylene torch, then it cut fine.
From there on, it was a matter of fine-shaping and finishing. On and off for the next week, whenever I wanted to pick up something to work on, it was right there, so I refined it a little bit at a time. When the shape was where I wanted it, I began polishing it with successively finer grits, starting at 80-grit (cutting to shape) then jumping to 120-grit, 400-grit, 600-grit, and finally 1000-grit hand polishing. The details up by the notch required the old “piece of sandpaper wrapped around a popsicle stick” technique for awkward surfaces.
That’s somewhere around 600-grit.
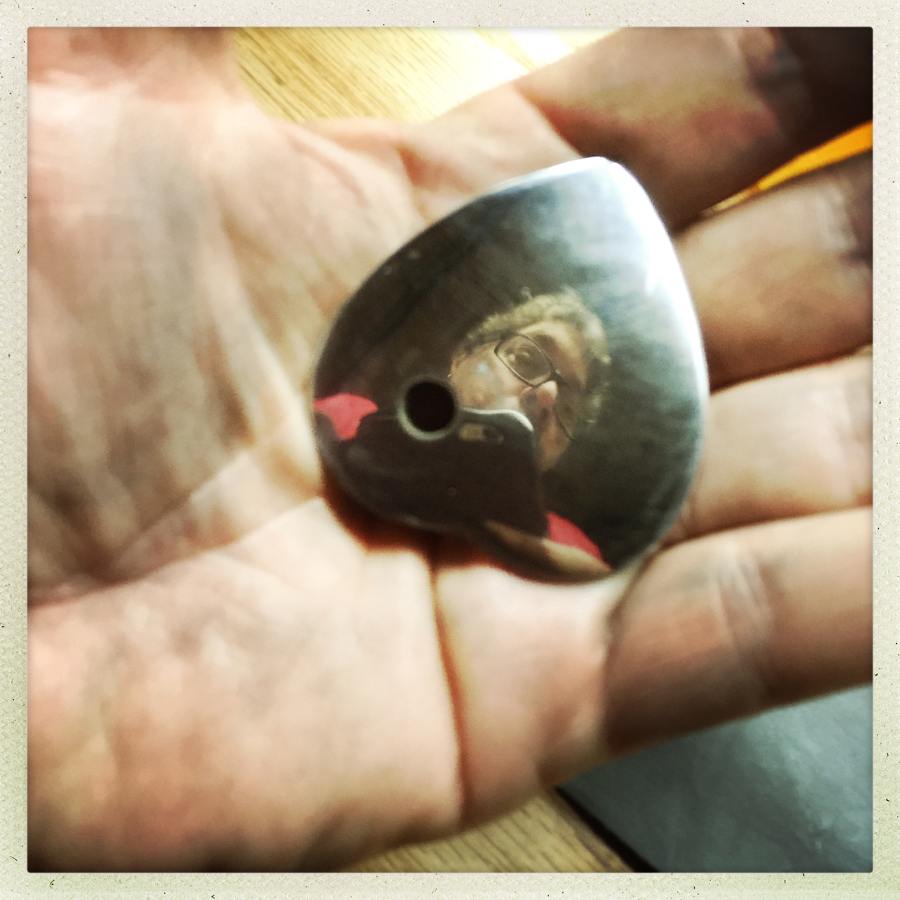
Self portrait, 2018
Then, at 1000-grit it’s ready to etch. Because I wanted to watch it carefully – it is about as exciting as paint drying – I took it home and hung it through the convenient hole, in a mug of ferric chloride.
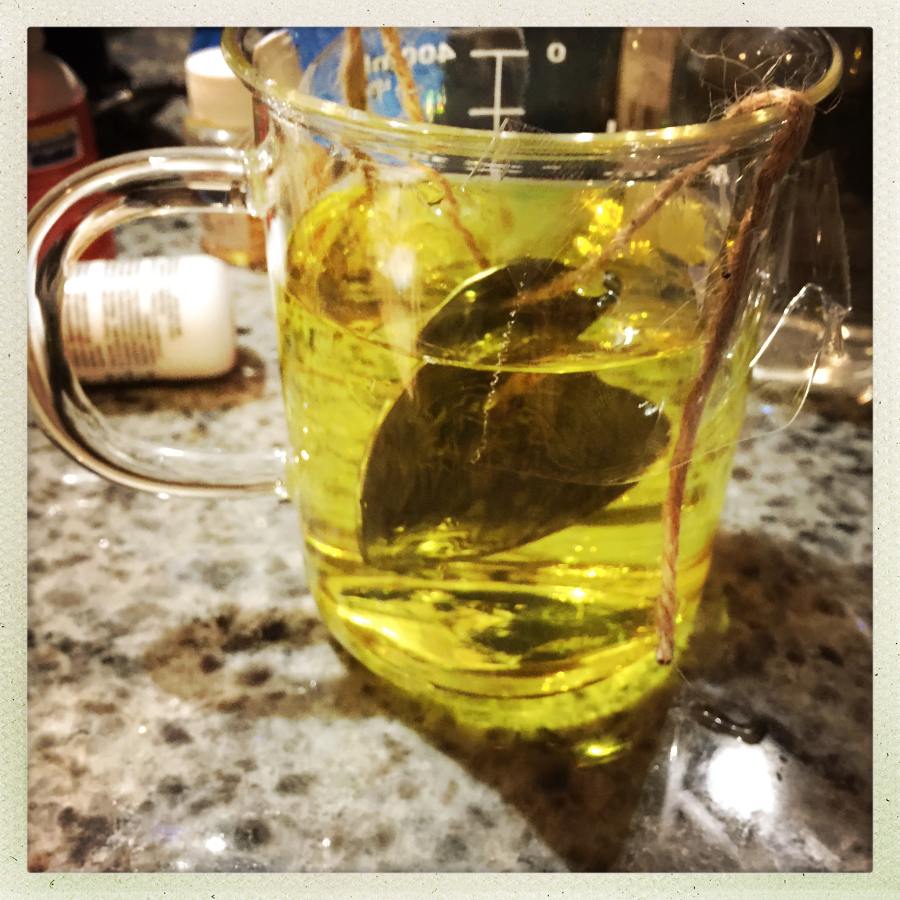
damasteel tactical tea-bag!
Some of my friends are into doing all sorts of weird things to color the metal; they swear by rubbing mustard on a work-piece, or whatever. I try to think about the underlying reaction (vinegar in the mustard) but it’s fun to play around. This brownish tint was a result of letting it sit in boiling coffee for an hour. “erasing” a finish is simple; just steel wool it or drop it back in the ferric chloride.
I made a little felt bag for it out of some scraps, packed it up, and mailed it off to Kestrel. From there, the story is hers to tell.
I call these things “goobies”. FYI.
During the grinding and polishing, the steel got heat-cycled and cooled many times, so it is quite hard. It’s not hard enough that it risks shattering; it’s just tough as can be.
Purty, but it may be the world’s clumsiest guitar pick.
Nice.
Beautiful.
Reginald Selkirk@#1:
Guitar pick would be doable…
Lovely but I am not dropping over for a cup of tea.
I love the grain in the metal. So cool that doing something as mundane as boiling it in coffee brings out the beauty.
@Marcus, #4: Talk about “heavy metal”! Although… I know that Brian May uses a coin for a pick, so hey, maybe you are on to something here! I know some people who would give such a product a test drive…
Very cool, in many ways.
Can you tell us some more specifics on the action of the ferric chloride? Is it just a selective oxidizer, to bring out the variations, with different colorings?
Bruce@7:
The ferric is a generic oxidizer, I think. Not sure why bladesmiths use it instead of something more aggressive – I suspect it’s “tradition” since it was easily obtained at Radio Shack for etching circuit boards.
I brew my own by dissolving a pad of steel wool in a liter of muriatic acid, then cutting the results with a liter of 3% hydrogen peroxide.
The ferric is slow and gentle and it gives good contrast. Now I’m going to have to experiment, I suppose… I’ve already had some fun dunking damasteel into copper sulfate, which slightly copper plates it, then into selenium toner, which gives an exotic blue-black.
The darker brown is the 1095 high carbon, and the brighter lines are 15N20, which is also a high carbon steel but contains some chromium in alloy.
I’ve added “guitar pick” to my “todo” list.
Beautiful, and yay for seeing the heart. Looking forward to seeing what Kestrell does with it.
@Marcus, you should be able to do ferric chloride also by dissolving rust or scale dust directly in muriatic acid and reduce or completely cut the peroxidek, because iron in rust is already oxidized to max, and in scale it is oxidized like 60% to max. I have never tried this though, I bought my ferric chloride done.
Any acid will etch the steel, originaly damascus was etched by citrus juice. The discolorations are not only due to buildup of various oxides though, but also due to dissolving some elementss (iron) whilst leaving others behind (chromium, nickel, carbon, silica), and by dissolving/oxidizing on crystal boundaries faster than on facets due to electrochemical gradients on said boundaries (this causes pitting in mono steel).
But some acids are lousy at etching, because they are too effective at dissolving (like pure muriatic acid). Some are so good at oxidizing, that they are lousy at etching (like hot, concentrated nitric acid). All acids were not created equal.
Which is why very dilluted acids should be used for etching damascus, otherwise the corrosion is too uniform or too quick or both.
Too big for a guitar pick, unless you have a really big guitar.
Might work well as a dobro bar or slide. Most are straight but why knows what advantages a heart-shaped bar might have.
It is lovely, and for some weird reason your heart and Caine featured in my dreams last night.
The companion piece, The Heart of Caine, written by kestrel is now up at Affinity. https://proxy.freethought.online/affinity/2018/12/22/the-heart-of-caine/#more-35625