Why do steel sparks do this thing: they fly straight and seem to explode at the end of their trajectory.
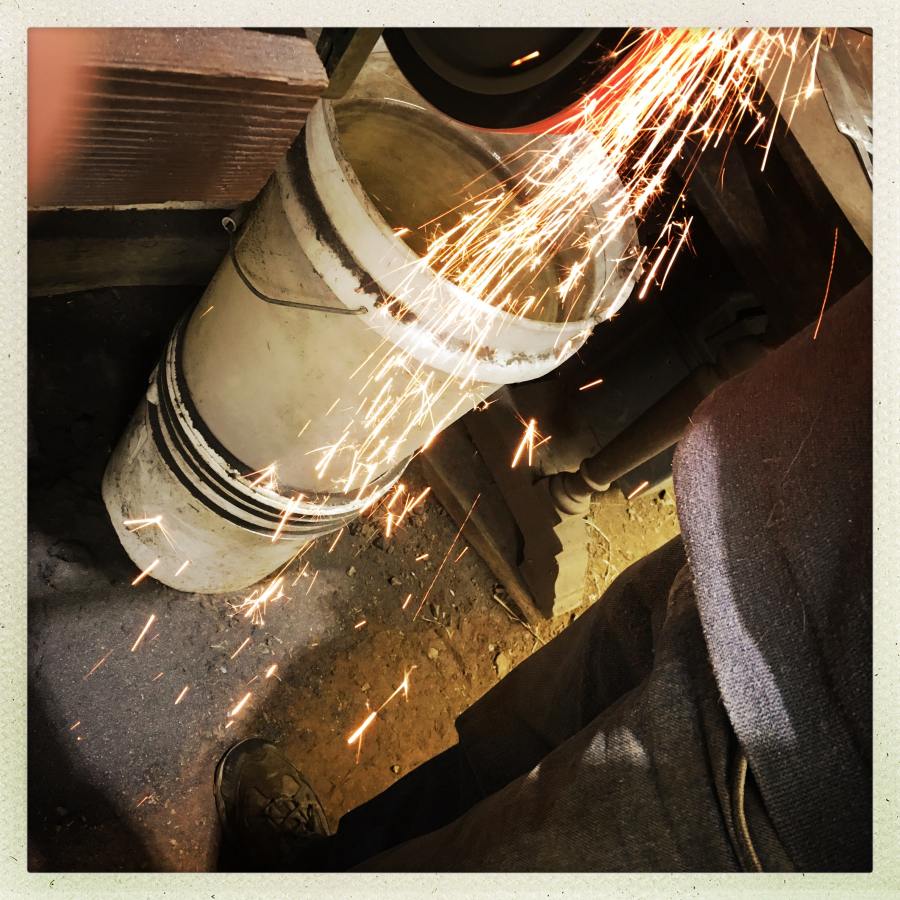
Steel sparks off a grinder like time flies like an arrow
The spark makes a line, then there’s a little star-shaped explosion at the end and it goes dark.
My suspicion is that the steel is oxidizing and it heats up more as it goes through the air, finally getting hot and breaking into pieces. If you look at the two sparks center-left you’ll see what I mean – there’s a line and then it looks like it’s breaking into 4 or 5 fragments. I’m guessing that, at that point, they no longer have enough thermal mass to stay at radiant temperature and go dark.
Anyone know? It’s not as if this is important, but it’s something I’ve wondered about at a low level on and off since I first saw someone grinding steel. It doesn’t work for all metals, e.g.: copper or brass (I’ve ground my share of brass) so it’s got to have something to do with oxidation?
Does pure iron without any carbon spark?
As kids we used to burn steel wool, finely divided steel burns quite nicely given the chance.
Pure iron makes sparks but the sparks don’t explode at the end like carbon steel does. You can verify this with a hunk of cast iron and a bit of spring steel. You can tell a lot about steel by the sparks it makes. https://en.wikipedia.org/wiki/Spark_testing
Oh, and according to my old shop teacher back in the ’70’s, you are right about an exothermic reaction in the fragments. It takes a lot of energy to grind off bits of steel, so they’re hot enough to burn in air once they escape the wheel. As they pass through air they get even hotter and at some point the carbon oxidizes with the steel which makes the little explosions. At least that’s what he said.
When I sharpen my Marshalltowns on the electric grinder, the sparks just go
straight out and vanish.
I’ve never seen a ‘splosion at the end.
Lofty@#2:
Yes! It’s very fun, except that I discovered it by accident when I threw a match into a pile of shop-floor sweepings and it got exciting for a bit (I stood and gawped while the red flame-crawlies wended around the strands) There’s a photographer, who I should find and do a posting about, who specializes in fine art photos of that sort of thing; they are incredible.
You can also use steel wool as a low-rent igniter if you short a car battery through it.
I have too wondered about this and my reasoning is this:
Because the sparks fork and explode more and more in correlation with carbon content, I think it is caused by the way it oxidizes, not heat alone. Both iron and carbon oxidize in exothermic reaction, but however counterintuitive it is, carbon is actually slightly harder to ignite than iron. So in the particle first ignites the iron, then it gets hot, then ignites the carbon and that causes the spark to explode, because carbon oxides are solid, but carbon oxides are gasses.
The only reason coal/charcoal burns is because it is porous, the product is gas that goes away, and it requires constant influx of oxygen in order to do so. You would not be able to ignite a lump of graphite to self-combust in free air, the surface area exposed is too small and the oxygen influx too small to keep the reaction going.
And the only reason steel does not burn like charcoal is because it is solid and it forms a layer of protective oxides. Steel wool is actually very easy to ignite and particulate steel can even explode when mixed with air.
Georgewiman@#3:
Pure iron makes sparks but the sparks don’t explode at the end like carbon steel does. You can verify this with a hunk of cast iron and a bit of spring steel. You can tell a lot about steel by the sparks it makes. https://en.wikipedia.org/wiki/Spark_testing
Aha! I had seen the effect sometimes, but not always – I must have been using different steels. I first noticed it when I was in high school, grinding stuff, long before wikipedia. (Interesting how search engines change our knowledge acquisition; I probably could have gone to the JHU library and found a book on metallurgy but nowadays you don’t have to skim entire books) Thank you for digging that up.
I also hang out on the knifemaking 101 facebook group and people are often asking “what kind of iron is this?” – that’ll be useful.
It takes a lot of energy to grind off bits of steel, so they’re hot enough to burn in air once they escape the wheel. As they pass through air they get even hotter and at some point the carbon oxidizes with the steel which makes the little explosions.
(fist-pump) Science!
*iron* oxides are solid of course. Cursed typos.
chigau@#5:
When I sharpen my Marshalltowns on the electric grinder, the sparks just go
straight out and vanish.
You’re talking about a trowel? I’m betting that they have a higher manganese content (so they won’t rust as fast) and maybe that raises the ignition temperature of the pieces the grinder knocks off.
Charly@#7:
You would not be able to ignite a lump of graphite to self-combust in free air
Not generally; apparently at Chernobyl one of the reasons it was such a mess was because the graphite mediator was hot enough that it ignited and the combustion byproducts were nasty radioactive stuff. Although [energycollective report] doesn’t seem to think that’s what happened (it flies right over my head)
And the only reason steel does not burn like charcoal is because it is solid and it forms a layer of protective oxides. Steel wool is actually very easy to ignite and particulate steel can even explode when mixed with air
I didn’t know about the protective oxide effect; that’s cool. Steel powder and potassium perchlorate is almost as good as aluminum powder. Or, at least, that’s what a friend told me once. (cough) (cough)
@Charly #7
Iron does not form a protective oxide layer like for example aluminium or titanium, independent of carbon content. Thats the reason why iron, steels and even cast iron* are rusting, because the layer of rust (iron oxide) is permeable for oxygen. A good rule of thumb is: If you can see the (natural) oxide layer with the naked eye, it is non protective.
The most common steel is building steel, which has a rust layer the second it comes out of the foundry. You can see it on any construction side, where there are huge piles of rusting steel waiting to be put into a protective layer of concrete.
Refined steels rust to, but very slowly, because they are very pure. That means that besides carbon and wanted alloys there are very little unwanted impurities in the steel, which helps to reduce the oxidation rate.
Non rusting steels are high alloy steels. The most common way to make a steel non rusting is to alloy it with at least 13 w% chrome. Chrome, unlike iron, forms a protective oxide layer, and 13 % are enough to keep the entire surface of the steel protected.
Cast iron is also rather slow rusting. Mostly because it has a very high carbon contend. This high carbon content slows down rusting, because it reduce the available iron surface.
*The difference between steel, iron and cast Iron is the carbon content, measured in per cent of weight (w%).
If you have 0-0.022 w% carbon content it is called iron, 0.022-4.4 w% carbon content is called steel, and 4.4-6.67 w% carbon content is called cast iron.
Correction:
0.022-2.06 w% carbon content is called steel, and 2.06 – 6.67 w% carbon content is called cast iron. 4.3-4.4 w% carbon is the eutectic point of iron-carbon compositions, which means it is the composition with the lowest melting point. I always get these two points crossed in my head.
Thats why i should always check the phase diagram before i post a comment.
@Turi1337
I beg to differ.
You are talking about corrosion, I am talking about combustion. Those are two different things. Even so.
The oxide layer that forms on steel in mill (and on anvil) is magnetite (triiron tetraoxide), and it Is protective enough to shield the steel from ignition and spontaneous combustion. Even a layer of anhydric iron(II) oxide is protective under these circumstances, that is why iron grates in stoves are even possible.
It even protects the iron from rusting, which is why it is not always removed afterwards, but left on (depending on the product and its final use/destination).
It just is is not as protective in long term as chromium or luminium oxides, because it is brittle and cracks due to temperature changes and once that happens, it is essentially over. So it allows in long term air oxygen and moisture to gnaw at the metal and react with it at room temperature and form iron hydroxides and carbonates – and those are rust. And because they have higher volume than the metal, they cause the mill scale to flake off, thus .
However rusty iron can be stabilized by boiling, which converts the hydrides into a layser of hematite. And that slows corrosion.
If you do not believe me, polish two pieces of steel with coarse sandpaper. Heat one up to red hot, let it cool and do not remove the layer of oxide that builds up. Then let them both overnight outside and see which one rusts more and faster. My bet is on the polished one for a while, but in the long term they both end the same.
This has sparked my curiosity so I went on a short google-limp during snack. And I found this. I knew since school years that iron wire burns in pure oxygen atmosphere, so what caught my attention in this article is this (emphassis mine):
In air the oxygen cannot reach the iron fast enough for such high temperatures to be sustained, thus the oxide layer keeps its protective properties and the wire will not combust.
@Charly I see where this is coming from.
You are right that the oxide layer would protect against combustion, because it reduces the rate of oxidation of the iron surface layers under the rate needed for a sustained combustion. Similar to how ash reduces the rate a brick of coal burns or a layer of earth prevents wood from burning up in charcoal production.
What iron does not do is build a protective oxide layer. The layer of iron oxide on the iron surface is always permeable for oxygen even before it cracks. Which it will do because the formation of iron oxides also results in a volume increase that breaks the surface up when it gets thick enough.
There is an entire class of metals called iron metals just because of this attribute (which is rare in metals). This layer can slow down the rate of oxidation but not prevent it.
Its a terminology thing, where protective oxide layer has a very specific meaning in material science.
Concerning to your experiment: The results would highly depend on the used steel. If it was a building steel you could be right, because the oxidation layer reduces the oxidation rate, unless you make it “fair” by reducing the oxygen pressure for the blank sample.
But if it was a refined steel, your already oxidized sample would rust much faster than than a blank piece of steel. Oxidation of iron in corrosion depends on localized differences in chemical potential of the surface. These lead to a electric potential which facilitates oxidation. A refined steel has, because of its high purity, very few of these different chemical potentials, while a oxidized sample will have lots.
When you’re grinding, you’re constantly exposing steel that hasn’t had much time to oxidize.
@Turi1337
I read up on the issue to refresh my memory and I think our disagreement lies more in our understanding of english techical terminology, rather in our understanding of the underlying chemistry.
Mill scale is not permeable for oxygen per se, but it breaks and once a crack builds, in that area starts localized corrosion and pitting. Hematite is permeable for oxygen and moisture, but it slows the rate at which it reaches the surface so it protects the surface slightly in not too wet environment. That is why old axes, scythes etc. have dark surface, but they do not build flaking off rust even when stored in the barn where the temperature fluctuates.
The worst that can happen to steel is a build up of unstable hydroxide layers and/or having patchy coat of scale. Hydroxide layer is hygroscopic and greatly accelerates the corrosion and flaking off. The edge of mill scale builds de-facto a microscopic cell and accelerates corrosion in that area (similarly to when one tries to attach copper directly to steel – or when one dunks steel nail and copper wire in vinegar and connects them outside – it makes electric current and the steel corrodes very rapidly – yay for childhood experiments!).