Finishing up the Japanese-style cleaver mounting…
Next up, the main handle block gets marked and clamped up in the vise on the drill press. A line of holes is drilled, which are then hogged together with a long mill in a dremel tool.
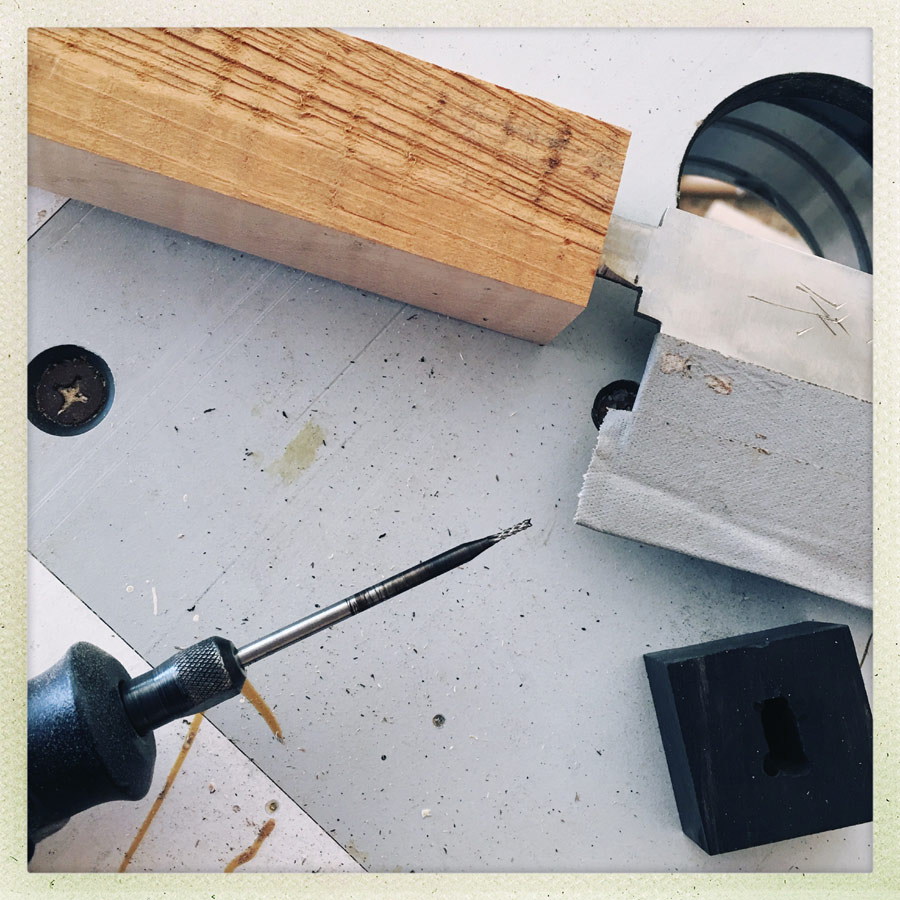
handle block drilled
At this point, everything is ready to be glued up. The interior of the handle is pretty roughly hogged-out so that there will be plenty of surface for the epoxy to bind to. I take the blade tang (the back piece that goes into the handle) over to a sanding drum and expose some clean oil-free metal for the epoxy to stick to. That’s really important – one of my first mountings came apart and I swore it would never happen again.
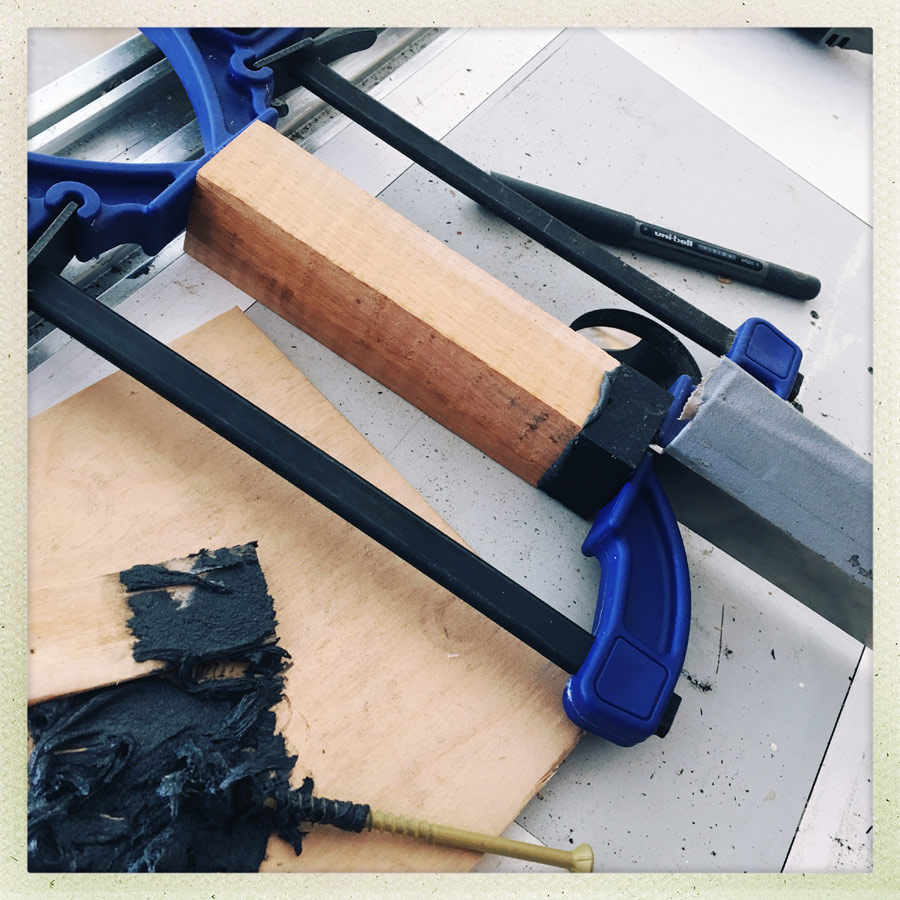
pc-7 and clamps
Since I want this to match the ebony, I mix a tiny bit of fiebing’s black leather dye (which is basically carbon pigment and alcohol) to darken it, then pack the hole in the handle, and coat the tang as completely as possible. You know you’ve got it right when you clamp the whole thing together and epoxy comes squishing out: you want the interior completely sealed. Then, let it sit a couple of days while the epoxy cures.
One time, I got over-enthusiastic and started finishing a knife before the epoxy was cured. The whole mess came apart in my hands from the vibration as I buffed it, and I had to clean it all off and start over. Ugh.
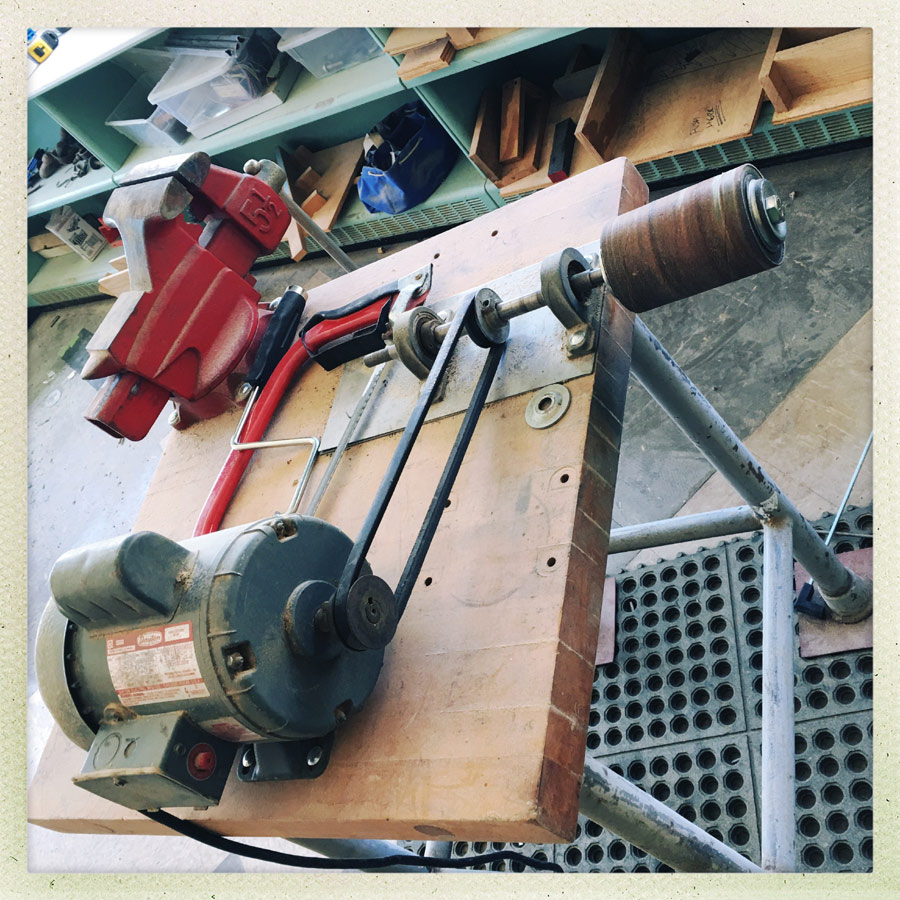
knife bench machine
Professional knife-makers use a 3-wheel belt sander, which is much more convenient. I made this machine when I was in high school and have been hauling it around ever since. It’s a sanding drum on a mandrel, powered by a washing machine motor (originally: I upgraded to a table saw motor when the washer motor died) The steel plate under the mandrel blocks keeps it straight so the bearings won’t burn up, and the drum won’t vibrate. It’s a good set-up except there’s a couple angles that are a bit hard to get at, whereas the 3-wheel sanders don’t have that problem. I could buy one of those but… why?
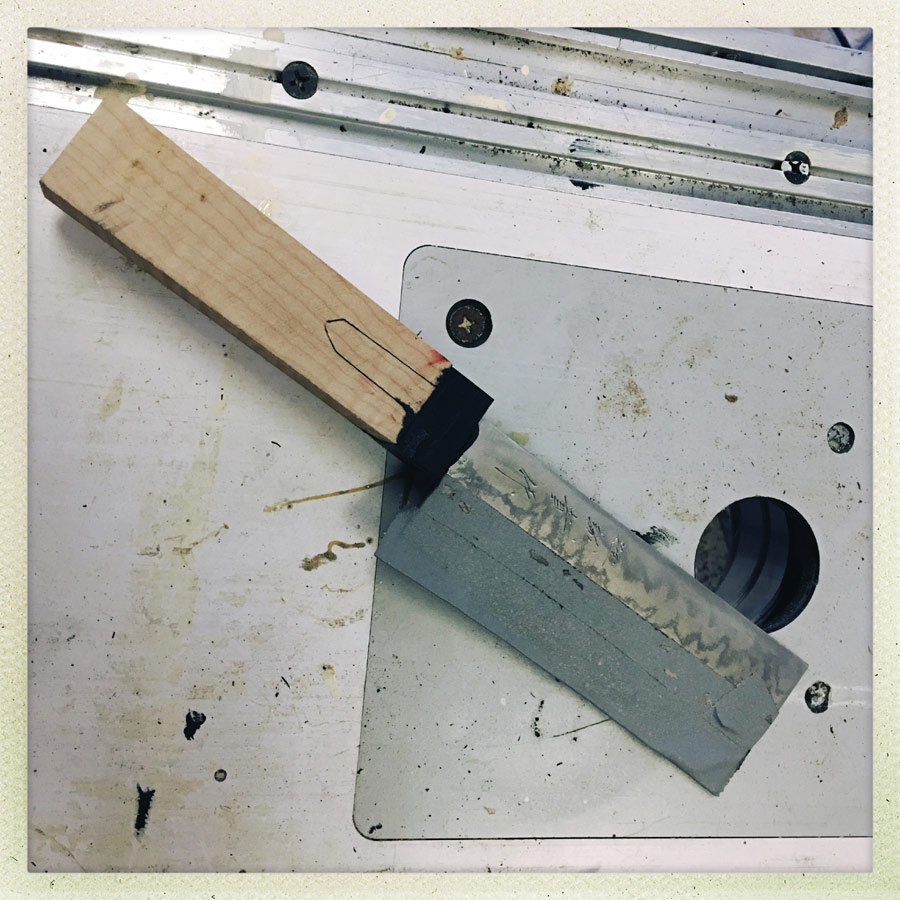
ready to shape the wood
This is where the tape on the blade is really important. If the wheel binds on the handle, or your grip slips, the knife can shoot across the room and may take part of you with it. Also, if you hit the blade on the sanding drum, it’ll take a chunk right out of the edge and it’ll take hours to reshape the edge and re-polish the blade.
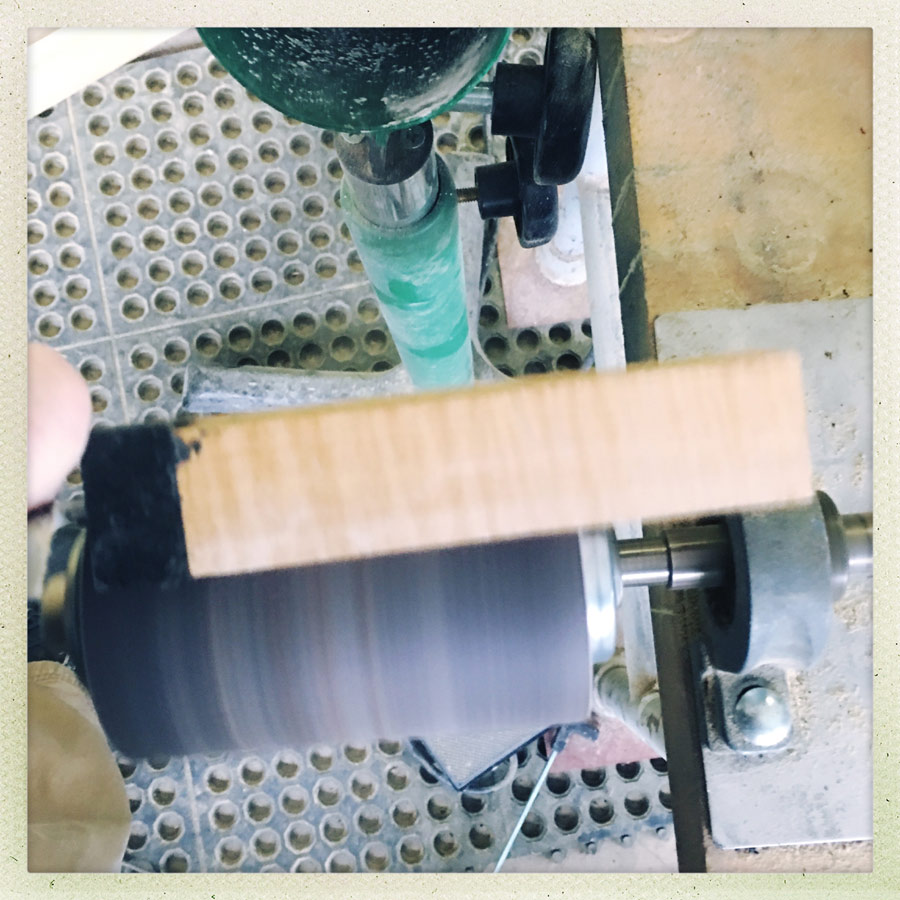
shaping the wood
A decade ago I got tired of wood-filled boogers and got a dust control system. The vacuum inlet is right at the top of the sanding drum. This was a difficult photo to get – holding iPhone while trying to sand. Normally it looks really cool, the sawdust comes off like smoke; it cuts very fast even with fine abrasive. The whole shaping process is pretty quick – about 15 minutes. You just hold the blade (carefully!) and keep rotating it and removing wood evenly until it feels right in your hand.
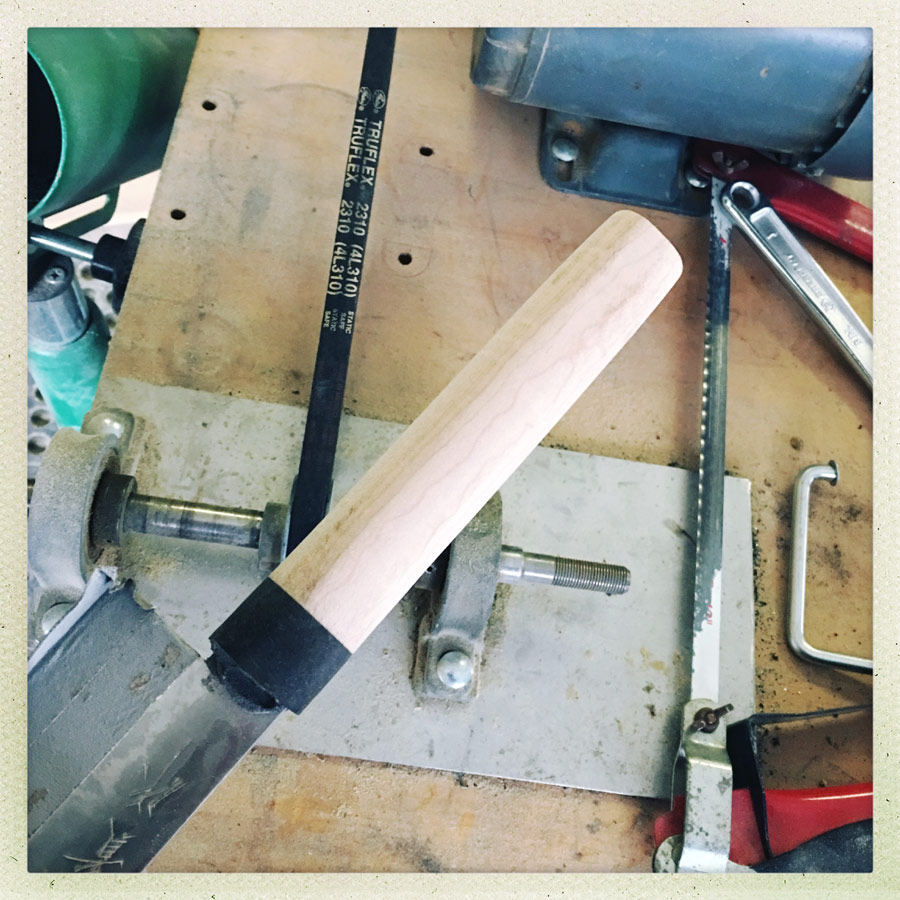
pretty close to done
I fine finish with a lot of sandpaper and steel wool. When I shape the handle I go for “feels right” and I think hand-sanding gives you hand-shaped handles, which is ideal for something you’ll be holding in your hand.
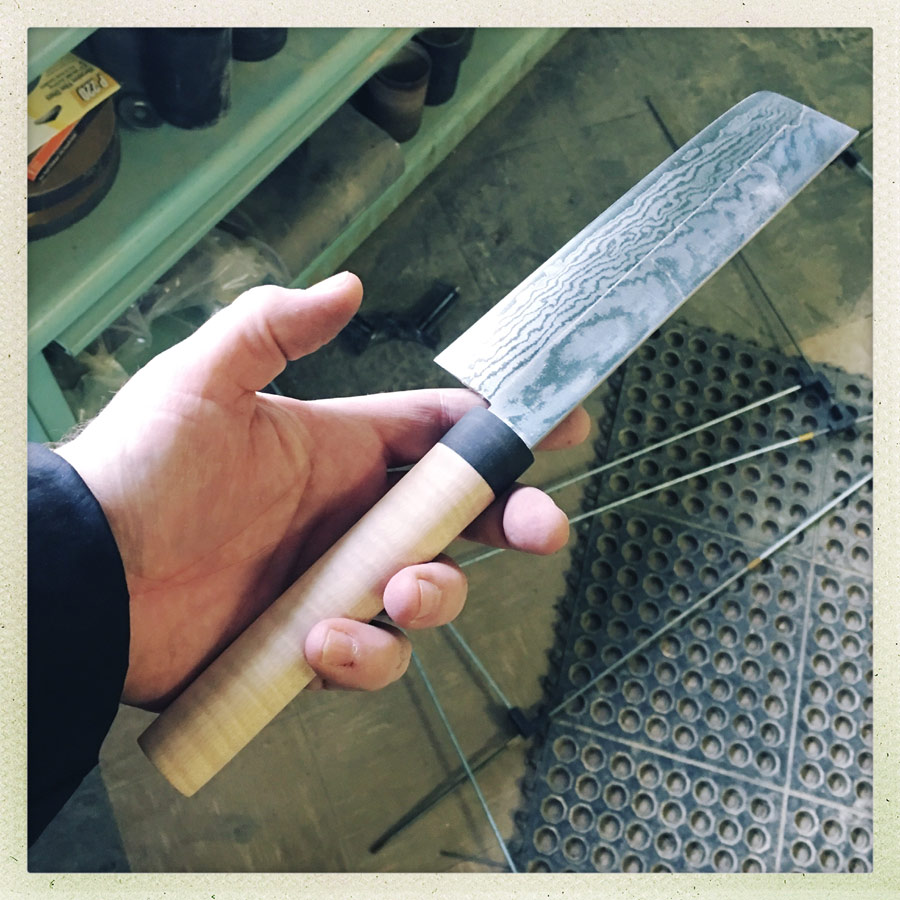
fine finish

buffing
The last stage is the one that scares me the most. I put a felt wheel on the arbor and load it up with abrasive cream, then burnish the blade very very carefully. If the felt wheel grabs the blade, it’s gone – because I hold it just with a couple fingers so that I have nothing in the line of travel if the blade catches. The objective here is to match the steel of the older knife, which has about 10 years of use on it and is burnished to a beautiful patina.
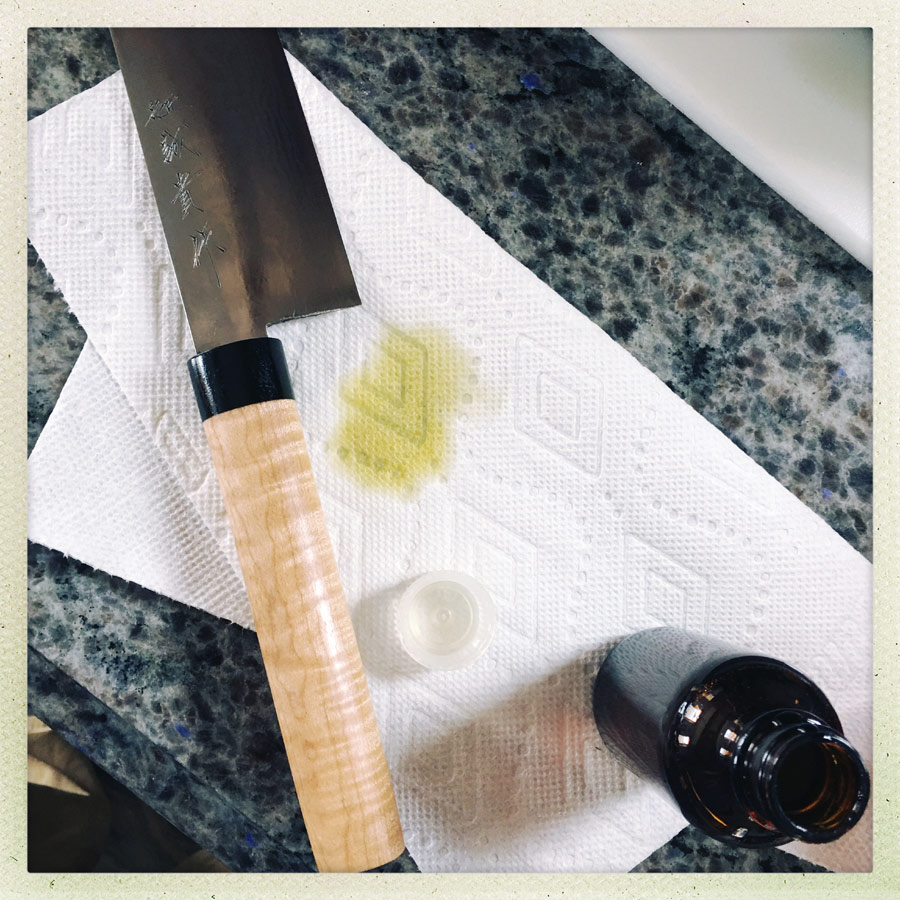
linseed oil
Japanese chef’s knife handles are unfinished (which makes them less durable) so I soak the wood with linseed oil. That’s a classical “French rubbed finish” – you take a drop of oil every day for a week, and stretch that single drop of oil all over the wood. You actually can do it, it just takes some rubbing.
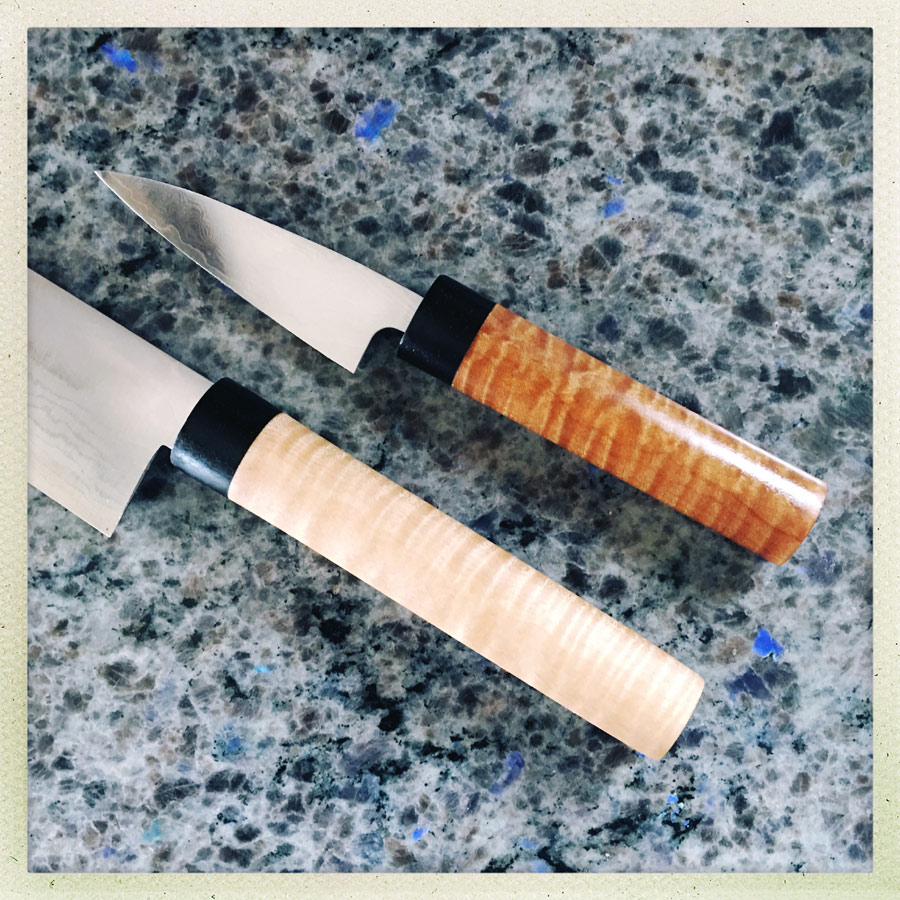
oiling the handle
After about 10 coats it will suddenly start to glow. The handle on the upper knife is 10+ years old, and has aged nicely. The lower knife will age to match in about a month or two. For now they look different but they’ll look like old brothers soon.
If you want to sharpen a knife so it’s scalpel sharp, I recommend a diamond impregnated steel block. You can get them here. I put mine on my counter, with a silicone baking sheet under it so it won’t slip and water won’t get all over – and most importantly – my hand is nowhere near holding the sharpening block. The reason I like diamonds and steel is because the block will never lose its shape. For 20+ years I sharpened on a Japanese ultra fine stone block and eventually the block started to lose its flatness and I bought the diamond steels to re-level my stone block, and finally realized that they were better than the stone block all along.
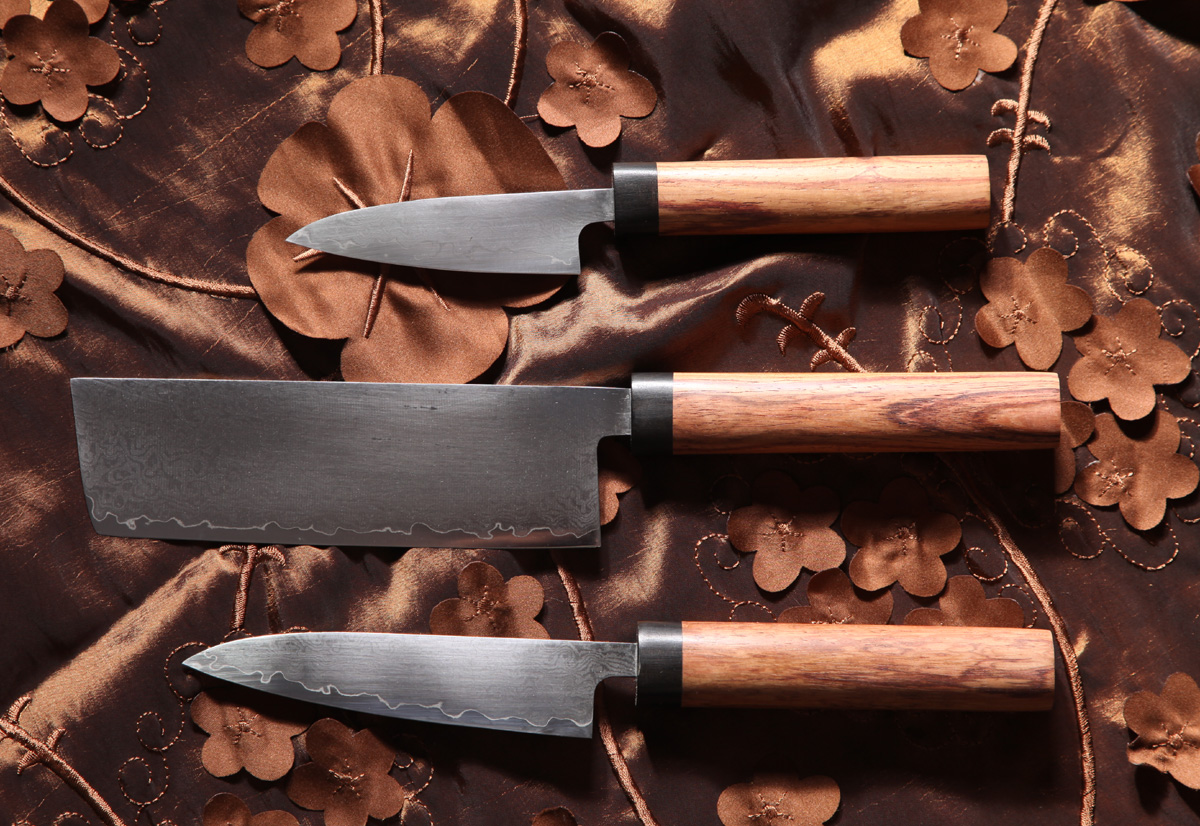
trio
This is a set I made back in 2008. They are ebony and honduran rosewood. To match the grain of the wood I sandpapered the blades and then buffed them in the same axis as the wood. I dunno if it looks better or not, but it felt like a good idea at the time.
Beautiful work. I was surprised you were able to take a photo while sanding! I don’t sand knife handles, but I do polish jewelry on a wheel and I know from experience how the wheel can grab whatever you are holding and fling it across the room with surprising force. Or slam it down onto the table. I wear big heavy gloves while doing this but that is partly because sterling silver gets really freaking hot when you polish it. I suppose this is not so much of a problem with wood.
I love the photo of the new knife and the old one… wow, the wood grain is so similar. Looks pretty fantastic!
Not black enough
Absolutely stunning, Marcus!
Lovely work, but I wouldn’t do it.
There appears to be blood on the uncarved block and you talk about near disembowelling in another post, and how dangerous it can be.
I’m clumsy, I’d manage to mangle myself quick smart.
Brian English@#4:
The red is actually from the paint on the throat plate of my table saw. Amazingly, I shed absolutely no blood at all doing this mounting, then proceeded to nick myself oiling the handle. The way the cleaver blade comes down in the front, there’s that really sharp square edge at the back near where your hand goes.
kestrel@#1:
I probably shouldn’t have tried sanding one handed, but anything for blogposterity!
I’d wondered about jewelry. And now I know! When you buff the blade it gets surprisingly hot. You have to keep the buffer off the wood or it’ll stain it. I used to use a little felt wheel on a dremel to polish the ebony but it turns out time and hands do the job well enough, and more safely.
Glad you like! Its new owner apparently has already fallen in love with it.
Caine@#3:
Thank you!!
BBC: Europe’s surprising knife capital