A voice from my past contacted me, and apparently they had been looking at some of my online postings, in which I mentioned that the skinny dagger I made for R.B.’s dad was a “letter opener” – she asked for a “husband opener.” Well, who could say “no” to that?!
[By the way, this has been done and shipped to its new person several months. So I know how it’s going to turn out, or I would not be posting this. Hint: no surprises.]
So, we talked a bit about what she wanted, and she said she had no clear idea except “wicked and elegant in that order” and “long and slim and very sharp.” and “in a celtic tradition.” Well. Shit. That sounds like it’s firmly in my wheelhouse. I’m not sure quite how that all clicked together in my head but I started thinking of it as the “Sean O’Rambo Knife.” So, sue me, it’s part of my creative process and the supreme court grants an exemption for any nastiness as long as it is part of a proper sincerely held creative process. Also, anything in a celtic tradition is an advance exemption to use lots of bog oak.
This is Sean O’Rambo, highland warrior.
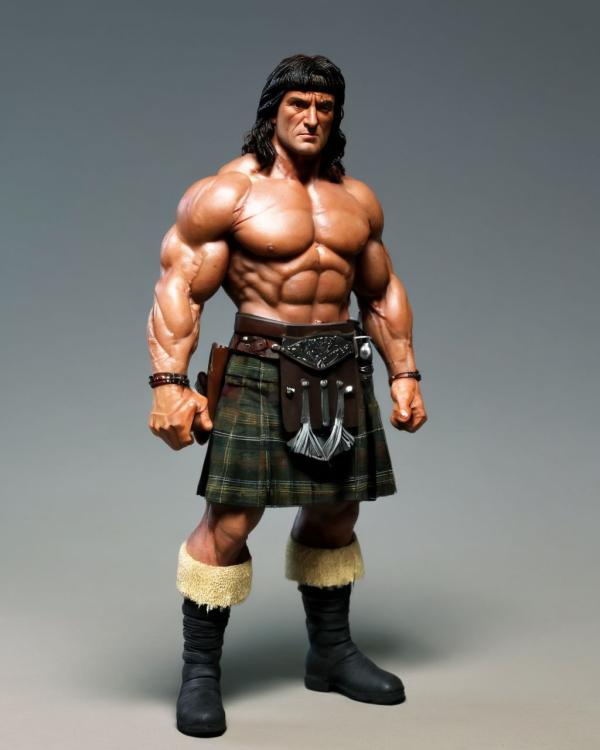
Sean O’Rambo, highland warrior by Midjourney AI and mjr
I decided there, and then, that I was going to be utterly uncompromising insofar as that I was going to make The Nastiest Piece of Steel I Have Ever Made. Now, I’m careful in my wording – this is not a competition with Kunihira [reddit] – but I decided there and then to be as nasty and evil as I could be, and to sacrifice blood, sweat, and tears to make this thing a righteous husband opener. Long, light, elegant, vicious, sharper than that piece of crap Stallone carried, practical, and with a nostalgic hint of The Morrigan’s influence.
Step 1: (you take a bunch of 3″ long 1/8″ pieces of 15N20 and 1095 high carbon steel, and surface grind them)
Then, you run a thick bead of weld down each end, using stainless steel welding rod. See, now, a few years ago I figured this one out: when you’re using a fluxed stick, whatever you’re welding’s going to be a puddle, right? So it doesn’t matter if you’re filling it with hardox or stainless or carbon – it’s stuck. But when the time comes to start making a knife out of it, you want to make sure you don’t have errant blobs o’the stainless in the surface of the thing. So the stainless is a simple indicator, and it’s frankly cool as shit to be able to use your metaphorical high voltage penis to ejaculate globs of stainless steel onto something and watch it melt and flow. (Yes, now that you ask, there was some vodka in my lemonade! Putin put it there!)
Who loves to play with fire? Sean O’Rambo does!
So, the big trick in forge welding is you want to get the pieces of metal close, then squish them a little bit so that they are even closer. Like, (this may not make sense) molecular close. Anoxic close. You want no gap of any sort between them. Then, at around 2200F (<- I don’t know what that is in French but it’s smaller) the crystals in one piece of steel begin to shake hands and do the shimmy shimmy with the crystals in the other piece. Then, after a good long soak in close proximity you haul it out and beat the shit out of it with a hammer. Then, it’s like a “shotgun wedding” the two pieces of steel become one, in holy matrimony. It’s very neat, as a process, because before you do the aforementioned shit beating there may still be a few molecules of carbon dioxide and other stuff between the pieces. When you whack them with a hammer, we are talking very small spaces and very small amounts, and considerable force: they break the fucking sound barrier trying to get out of the pinch that they are in. This is orgasmic for a blacksmith, when they hear the sonic boom. It’s less fun if they get a little squirt of 2200F flux on their leg but I have nobody in my life to concern themself about burn marks on my thighs, anymore. So, what.
A few whacks and then some smooshing in the hydraulic press (me not being an idiot) the steel consolidates itself into a single bar, but – because the properties of the steels are different (1095 oxidizes more readily than 15N20 with its higher nickel content) you can still see the stripes. How cool is that?
Actually, it’s not cool at all, it’s 2500F or thereabouts. Welding temperature is where I live. My good friend Anna, who is black, and from the south, wound up in Pennsylvania and does not like cold, complained about how fucking hot a forge is. I said, “sounds like it’s about right.” I’m of scandinavian extraction and start to sweat when it goes over 60F. We are not made for global warming.
After a bit of beating and smooshing the steel consolidates under the impact, stubbornness, scandinavian aggression, and heat, and becomes a homogenous bar of … stuff. Some people would call that stuff “damascus steel” but it’s not it’s “pattern welded” (damascus steel is wootz or oroshigane)
Isn’t it a thing of joy that an iPhone’s camera sees into the ultraviolet enough to register the heat coming off of that as purple? It’s that hot. Normally, like most of the priests of Festus (the god of the forge) I am stubborn about safety but I never wear synthetic shoes when I am working with forge welding. If that thing bounced off the anvil, landed on my foot, and stuck to burning plastic of what was left of my non-leather shoe, I would be like .. Haphaestus, gimp-god of the forge. I am a horribly stubborn human being but when pain hits, I’ll promise anyone anything to make it stop.
This, here, is an ambulance trip and a possible death sentence:
Back off, god, don’t you give me no lip [Anyone get the reference?] [Actually never mind, I was referring to Ronnie Hawkins but it seems like the Sex Pistols carpet-bombed that one]
Next step in forging is weird. You clamp the whole thing in a vise or use a cutter in a hydraulic press, to cut a reverse bevel to form the tip. So in the picture below, the curve of the edge is going to go from the bottom right up to the top. It’s weird how plastic steel is when it’s hot (unless it’s in the World Trade Center) you can hammer it and it feels like clay, at this temperature. So you put the angle point on the anvil and hit the overhang 1, 2, 3 heavy whacks, then put it in the press to flatten it again, then repeat. After 2 rounds of that you have a curve where the grain of the steel follows the edge. You don’t have to do that, but why on earth wouldn’t you once you know the trick?
The whole time I am doing this, what is left of my brain is wandering around thinking of the thousands of years and thousands of historical smiths who pulled this same trick of the mystery of steel. Sometimes it made them rich and famous, sometimes it got them tortured horribly, other times – they made a sword. It is endlessly weird to me to think that what I do so casually was probably a super secret military technique for a 900 years. [Shit this makes me think I should post something about the spear I recently finished, speaking of mysteries of steel]
I remember looking at that and thinking “oh, shit I have lost this one” but we always think that and we are always wrong. Those blobby edges will straighten true with a single tap of a hammer on anvil, the tip will come around, and in 15 minutes and a few more heats it’ll look like the knife it was always meant to be – by which I mean a great big blood-hungry long beast of a thing.
That’s for next episode. Once the blade is rough-shaped it goes into the annealing bin and cools overnight, then the next day I get the grinder on it and see what the metal looks like.
yesss can’t wait to see it
neat!
I wouldn’t mind hearing about the spear… (I’m sad that they are so undervalued (along with the shield) in so many rpgs/video games…)
speaking of spears, I keep having this borderline neurotic idea about a paired walking stick/trowel (I’m thinking something more like a hori-hori with a bayonet attachment?), that could serve as a hasty spear, for… reasons?a
I really need to finish building my next commuter bicycle before I entertain any other ideas/projects, I just need enough time off to recover, rest up, run errands, and have some time left over, which probably won’t happen until next winter holiday seasonish. :/
But, thanks for sharing these pics and posts. :)
That’s the world we are headed for.
When red-hot isn’t enough: New government heat risk tool sets magenta as most dangerous level
I love the mix of passion, science and raw emotion that makes cold steel.
Isn’t it a thing of joy that an iPhone’s camera sees into the ultraviolet enough to register the heat coming off of that as purple?
Isn’t this a case of seeing into the infrared?
Oooh, I do love your “the making of” posts. Also, yes the camera letting us see the purple heat is cool ;-)
“After 2 rounds of that you have a curve where the grain of the steel follows the edge. You don’t have to do that, but why on earth wouldn’t you once you know the trick?”
i have feelings about people who spend ages pattern welding but don’t do any actual forging on the blade (although considering i suck at forge welding i probably shouldn’t :P)
I’m excited to see the final piece
What Pierce said.
An IR crystal edge-emitting laser, with say nominal 840nm wavelength (the edge of our visual range is ~700) has enough output that it is visible red in a darkened room. The same laser in an iPhone camera is purple.
Pierce R. Butler@#5:
Isn’t this a case of seeing into the infrared?
You are correct. I had a brain fart (part of the process involves arc welding, which is ultraviolet, and I get confused between sunburn from the arc, and heat dizziness from the radiant heat from the steel)
dangerousbeans@#7:
i have feelings about people who spend ages pattern welding but don’t do any actual forging on the blade (although considering i suck at forge welding i probably shouldn’t :P)
I wish I had some pictures of that part of the process but it definitely takes two hands and I’m basically always alone in my shop. It’s a pretty trippy phase of the forging – you really realize how plastic steel gets when it’s anywhere over the temperature of burning jet fuel ;)
Marcus Ranum @ # 9: … arc welding, which is ultraviolet…
Good thing some part of it spills into the visible spectrum – would make a helluva challenge to work with only unseeable energies at that level!
Pierce R. Butler@#11:
Good thing some part of it spills into the visible spectrum – would make a helluva challenge to work with only unseeable energies at that level!
Oh, the molten hot dribbling liquid steel glows plenty.
Reminds me of a pretty amazingly unsettling video I saw once, of a Formula-1 refuelling accident. I guess they were running methanol or something ultra volatile like that, and the cameras didn’t pick up the flames at all – there were people scrambling around and rolling on the ground and beating the crap out of eachother for no apparent reason.
@Marcus
I’ll just picture my forging, but with more more skill and worse tats :P
Forging is amazing, reshaping steel with flame and my muscles
SchreiberBike@#4:
I love the mix of passion, science and raw emotion that makes cold steel.
I have similar feelings, added to a deep dusty layer of history. I constantly remember that this is one of the core technologies of history and I often get a chuckle when I realize that we really haven’t improved our processes dramatically in at least 1,000 years.
One could do a great version of a Kurzweil “singularity” chart on “hot metal working” starting with (maybe) meteoric iron and (definitely) gold and copper, then bronze, iron of various forms, steel, and… uh… there it peters out. Conclusion: we got a lot dumber around the 9th century except for a final burst when the Bessemer purification process was developed.
Probably even longer. I think that clickspring conclusively demonstrates that a complicated piece of kit like the Antikythera mechanism can be produced with relatively simple tools. Basically files, hand drills (with spade drill) a dividing plate and the scorper and trammel. All these are based on carburizing iron into hardenable steel.
Metal files are way more than a thousand years old, dating back to at least 1500 BCE in ancient Egypt.
Steel files dating back to the Roman period have been found. But I suspect they are a lot older. Steel was precious back then, so any worn out tool would be reconditioned or recycled. Most hand files are not that big. So it is questionable how well they would survive and be recognizable in the archeological record.
I would say that most of the innovations in the last thousand years were about scaling up. There are of course exceptions such as powder metallurgy.